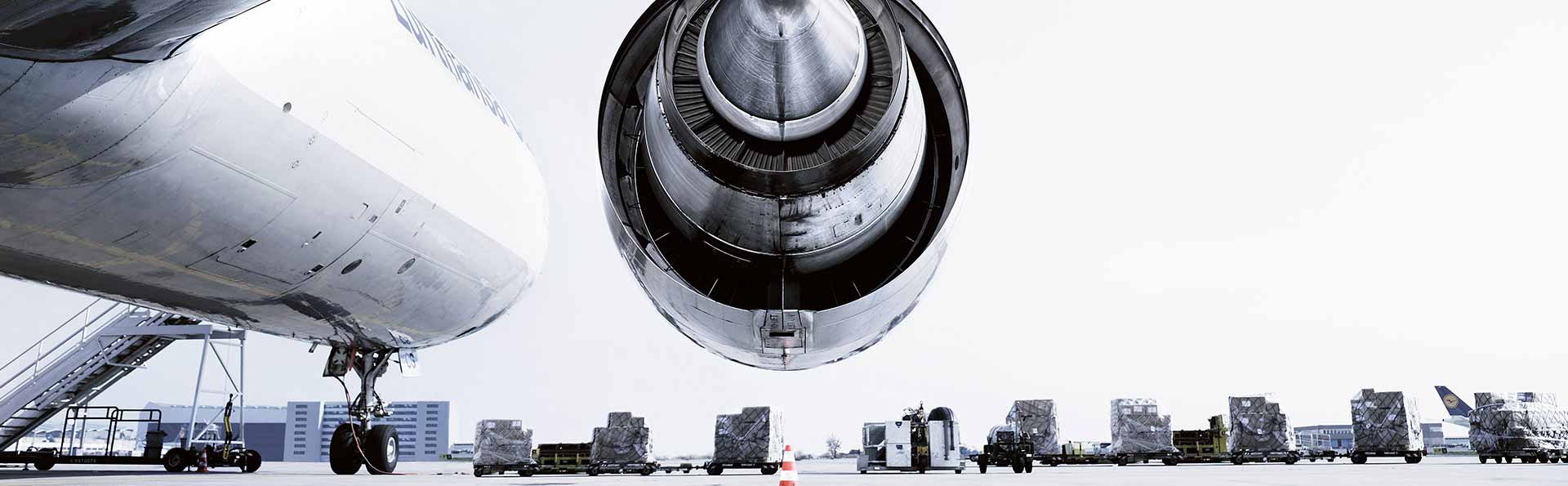
Dynamic control of the ramps and time slots
with procurement management
For the coordinated loading and unloading of its customers’ vehicles, Lufthansa Cargo is relying on
the dynamic time slot management system from EURO-LOG at Europe’s largest transhipment point for airfreight.
Starting situation at Lufthansa Cargo
Each day Lufthansa Cargo processes around 1,400 orders at the Frankfurt location and coordinates the loading and unloading of lorries at more than 90 bays.
Before introducing the EURO-LOG Time Slot Management the coordination of orders in import and export at the Frankfurt location involved considerable time and effort.
There was no IT based system which helped controlling processes at the import and export loading bays automatically. Slots and loading bays for freight deliveries, collections and road feeder services (RFS) were allocated manually after the particular vehicle‘s arrival.
Background information
Lufthansa Cargo has achieved cross-company transparency of arriving and departing trucks and their retention time. Thereby capabilities and parking spaces can be used as effectively as possible.
Due to notifications for all arriving trucks the processes at the loading bays can be planned in advance. The loading and unloading of more than 600 trucks per day can be coordinated more easily. Thanks to high quality data and transparency of the shipment structure both staff and capabilities can be planned in advance.
Lacks of capacity and long through times are avoided even in case of peak times.
EURO-LOG procurement management solution
For Lufthansa Cargo, dynamic time slot management means a reduction in process costs and better precision in planning. Time slots, bays and parking spaces can be planned in advance, helping to relieve the stress at peak times.
But the system also factors in actual levels of utilisation and reacts dynamically to changes. The system enables the overall planning of HGV movements to be done in advance on the basis of customer reservations or on the basis of the current flight plan. However, it is possible to make dynamic changes to the planning at short notice and at any time.
Bays are allocated dynamically according to current occupancy levels and changes to these. The EURO-LOG solution does not assign rigid time slots but allows for flexible rescheduling. This means that Lufthansa Cargo’s planning can be optimised to suit both its customers and its own processes. Customers can plan their transport operations more efficiently and view the current situation at the loading bays. This means that expected loading times can be calculated e.g. on the basis of the freight volumes announced and the loading equipment required for each slot.
The colour-coded display makes current data and important operating information visible to the employees of Lufthansa Cargo at a glance. The system also supports priority-based rescheduling. In addition, times for documentation processes are also included so that the total amount of time needed is known in advance. This avoids long waiting times for a space at the loading bay. In case of changes of plan, the customers of Lufthansa Cargo are informed in real time.
Time slots can either be allocated in Import and Export by employees of Lufthansa Cargo or reserved manually by customers via the Internet or via a system interface. The system automatically checks and confirms requests. All those involved have access to a standard system and time-consuming manual data inputs are no longer necessary as the dispatch data (AWBs) are taken from the existing Lufthansa Cargo systems to which the bay control system is connected.
When assigning the bays, the system factors in relevant information such as the type of transport (import/export), the volume of freight and the delivery and/or collection quantities and allocates a time slot on a bay with sufficient capacity for the HGV.
To do this the solution prioritises operations intelligently and automatically so that time-critical deliveries, for example, can be loaded as a priority. Parking space management is also part of the system so that the limited number of parking spaces can be used to best effect
About Lufthansa Cargo AG
Industrial sector: Air freight
Specification: One of the world’s leading air cargo carriers in international air traffic.
Route network: More than 300 destinations in around 100 countries worldwide
Fleet structure: 18 McDonnell-Douglas MD-11F
Employees: 4.609 (2012)
Sales revenues: 2,688 bn EUR (2012)
Internet: www.lufthansa-cargo.com
EURO-LOG Contact for Lufthansa Cargo
Claus Süskind
Head of Sales
EURO-LOG AG
Am Söldnermoos 17
85399 Hallbergmoos-München
Telefon: +49 811 9595-109
Telefax: +49 811 9595-199
E-Mail: c.sueskind@eurolog.com

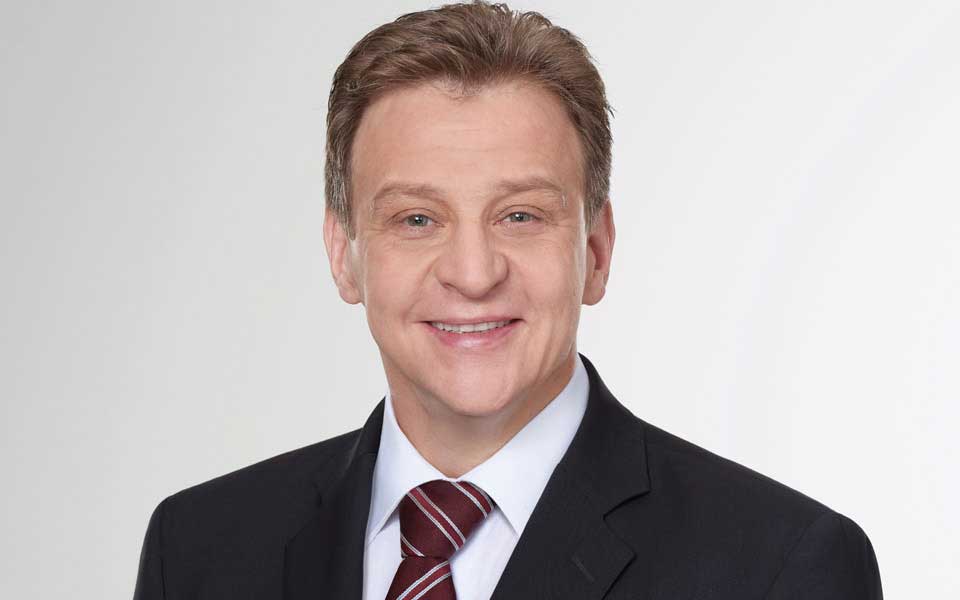
„With the help of EURO-LOG we achieved our goal, transparency over the entire transport network, in a very short time. Within one year a ROI was ensured.“
Armin Bergbauer, CIO Germany & Senior Director Application Development Europe,Ingram Micro Distribution GmbH

„The combination of container management and app helped us to make our container management processes simpler and shorter.“
Thomas Kraft, Managing Director Logistics, HYDAC Verwaltungs GmbH
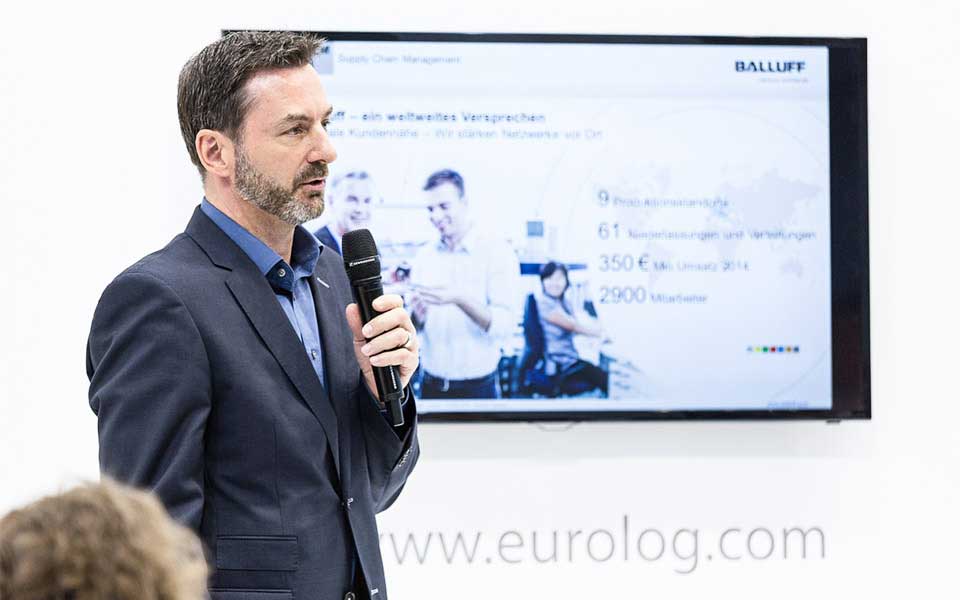
„By integrating ONE TRACK into our website, our customers can be specifically informed about a shipping via e-mail alert.“
Hondo Santos, Director Logistics, Balluff GmbH
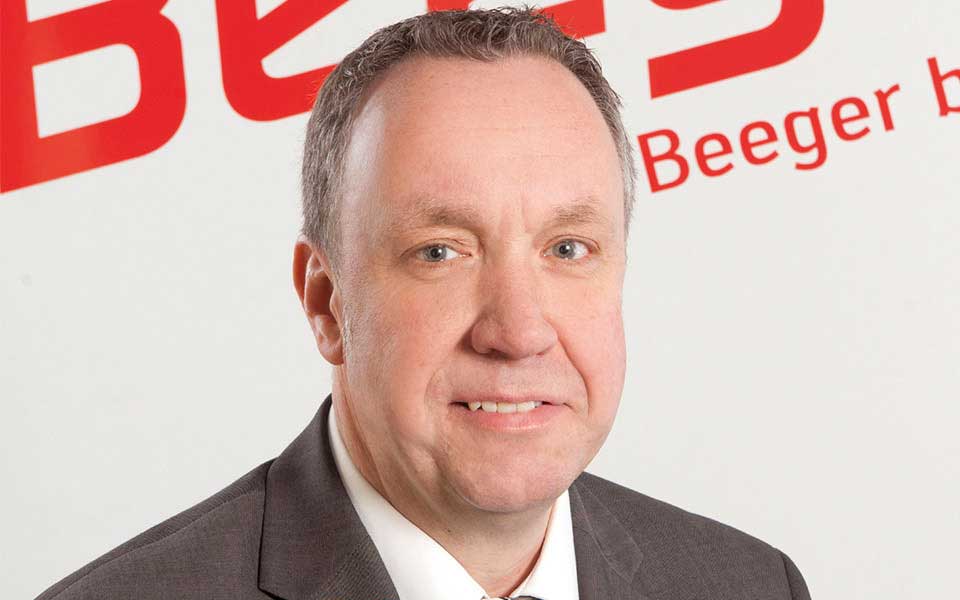
„The smartphones are much more cost-effective than our previous hardware. In addition, the app has been well-received by our drivers since it is very intuitive and easy to use with the clearly understandable icons.“
Frank Reichert, Branch Manager, Beeger Internationale Stückgut Logistik GmbH
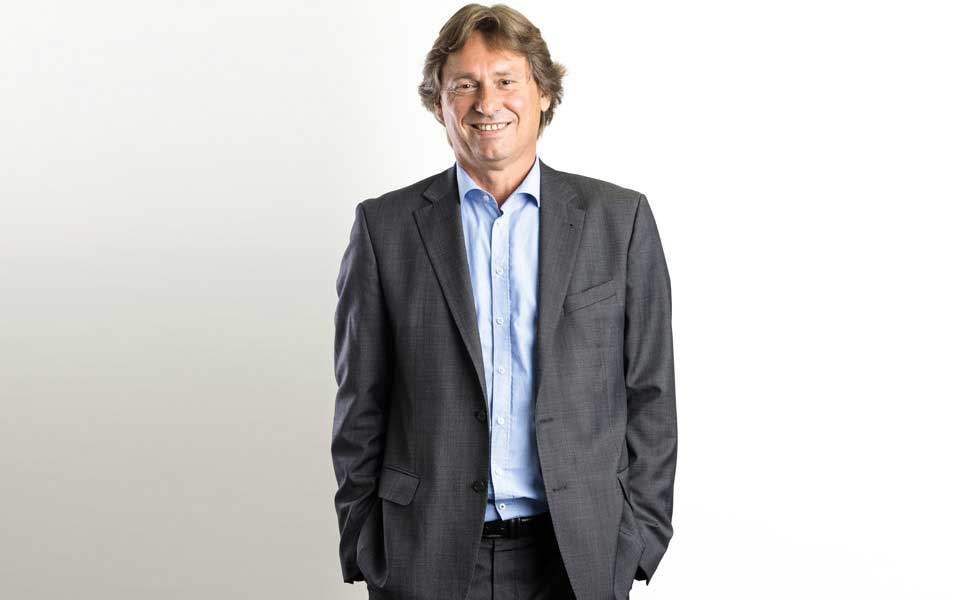
„Mobile Track enabled us to reduce our costs and save on the time and effort of our employees.“
Roland Gigl, former Managing Director, GS Frachtlogistik GmbH
Choose by solutions or industries

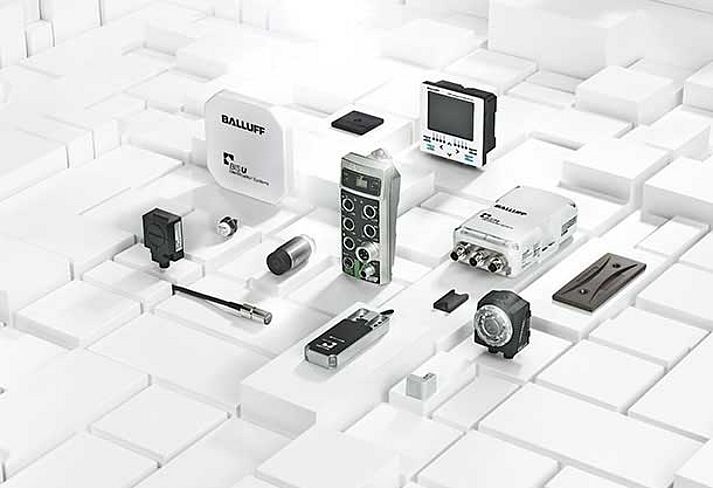
Balluff uses a standard monitoring system for the delivery times of its global transports.
Worldwide delivery time monitoring with long-term archive

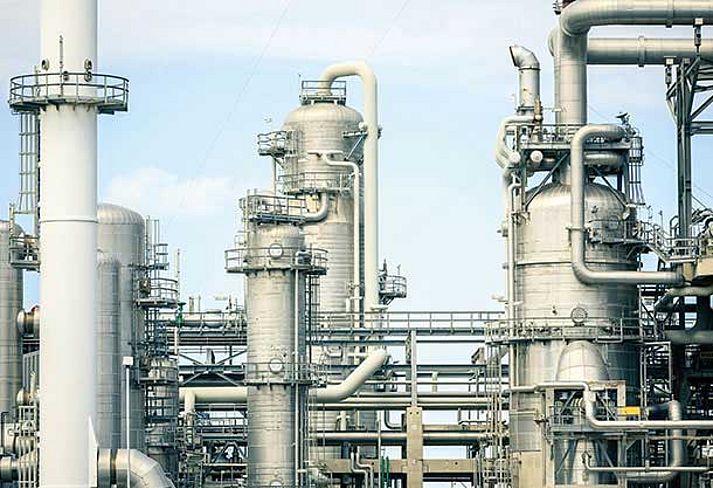
Thanks to the EURO-LOG logistics platform, clariant can flexibly integrate external logistics companies into the in-house sap system.
Clariant-SAP® talks to the systems operated by its service providers

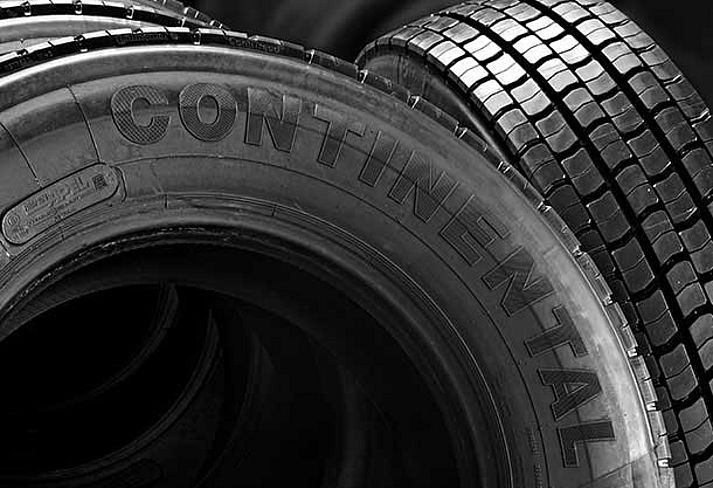
The aim of the Track & Trace project for Continental was to optimise customer service and to make communication with customers easier by improving the information base.
Europe-wide Track & Trace for greater customer service

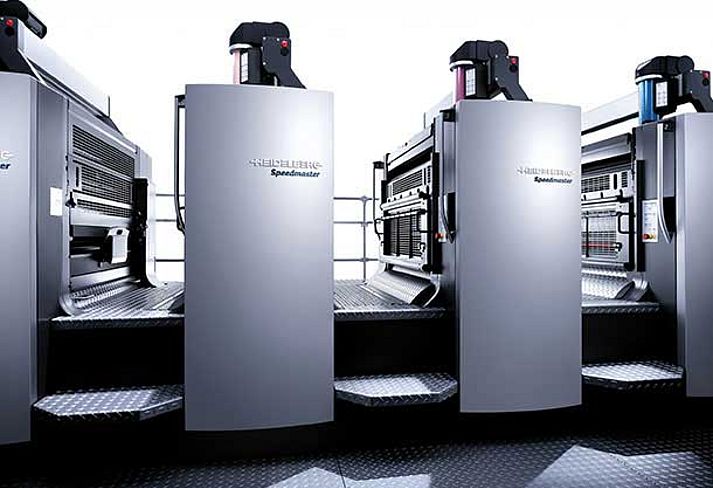
Heidelberger Druckmaschinen AG automates its goods inward flow with the EURO-LOG Supply Chain Management solution.
Automated procurement logistics with EURO-LOG


Digitalising the logistics chain creates the transparency needed to elevate cooperation between process partners to the next level.
Connect. Collaborate. Control. EUROLOG SCM Platform

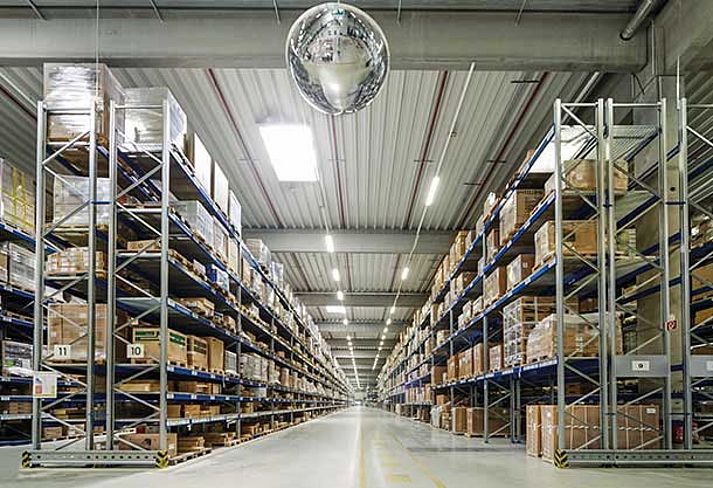
Transparent flow of goods, higher customer satisfaction and cost reduction: EURO-LOG transport management allows Ingram Micro and its customer to track the shipment status across europe in real time.
…
Zum Anwenderbericht The Case Study
Full transparency in the supply chain with transport management

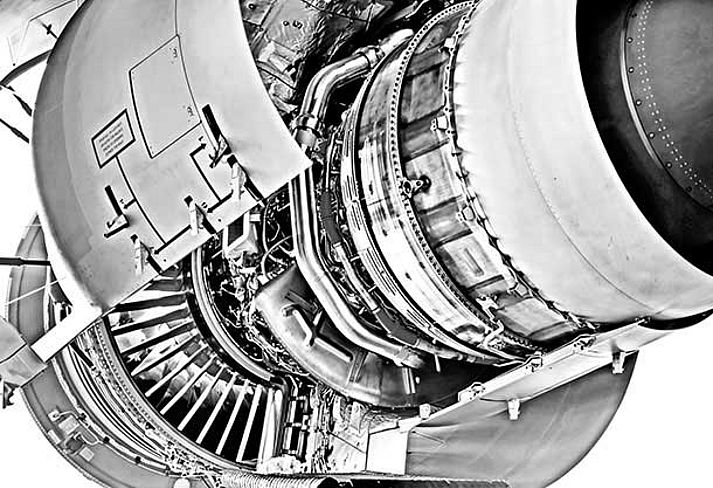
Lufthansa Technik Logistik Services services successfully uses a EURO-LOG AG real-time parts tracking system in spare parts logistics.
Worldwide track and trace in aviation spare parts logistics










EURO-LOG AG - AM SÖLDNERMOOS 17 - D-85399 HALLBERGMOOS - INFO@EUROLOG.COM - PHONE 0049 811 9595-0