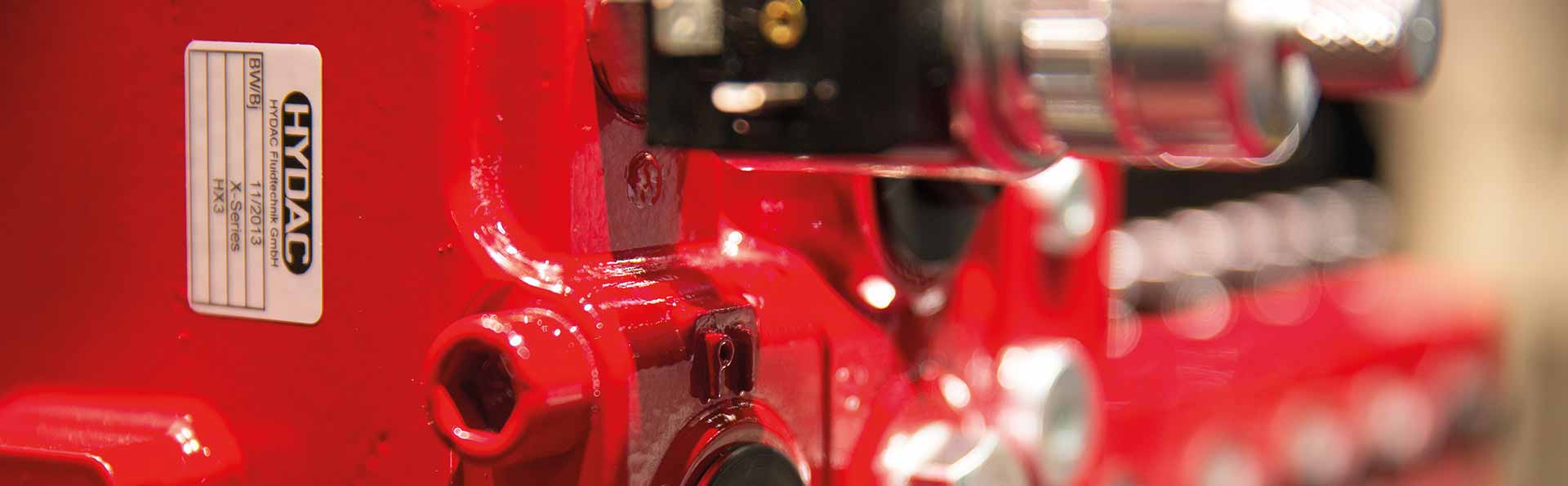
Comprehensive container management at HYDAC
HYDAC achieves a company-wide view of the physical inventories of in-house and customer containers
STARTING SITUATION AT HYDAC
The establishment of a central container pool for the standardised management of all containers was an important basis in this respect. The standardisation of the logistics processes of various plants was intended to enable a neutral appraisability. The use of mobile devices in goods inward was planned in order to automate manual data acquisition processes.
Before the start of the container management project, no comprehensive management of container movements and inventories was possible at HYDAC. Various stand-alone solutions were in place at the HYDAC sites, which were used to book the containers in the individual plants. However, there was no transparency in relation to the in-house pallet cages, small load carriers (SLC) and pallets, as the containers were managed in a number of different systems.
Cross-company container movements with triangular relationships were not able to be mapped in the existing systems. There was no clarity with regard to container costs, inventories, paths and connections between the individual HYDAC plants and the partners involved. The lack of transparency led to unnecessary costs, as unused inventories existed and containers often had to be purchased.
This led to a high percentage of tied capital and unnecessary storage costs. The lack of transparency meant that HYDAC recorded a high monthly loss of cage pallets. The loss was just as high for other container types. For example, thousands of small load carriers (SLC) were purchased every year.
Requirements profile
- Web-based, intuitive tool
- Mapping internal and external container movements
- Automation of container bookings
- Connection to customer portals
- High flexibility and development opportunities
EURO-LOG CONTAINER MANAGEMENT SOLUTION
The web-based solution means that the various HYDAC plants now have access to all container data in a central system. The system maps the container movements of HYDAC, its suppliers, customers and logistics service providers. Inventories, container costs and movements are available for all participants in real time.
The processing and retention times of the containers can be transparently tracked for all exchange partners. Only the load carriers actually in use are booked, so process deviations can immediately be identified. HYDAC suppliers and logistics service providers actively participate in the process: they have access to the tool and can book containers.
All partners can see the same data and have a joint data pool. Differences can be coordinated directly in the system, which enables close cooperation between the exchange partners.
The standard container management system now allows HYDAC to comprehensively control and evaluate the relevant logistics processes. The flexible reporting functionalities enable savings potentials to be identified and logistics costs to be reduced. The loss of containers and the purchase of new containers was able to be permanently reduced.
INTEGRATION OF MOBILE DEVICES
In goods inward, the integration of the digital pen significantly facilitated and shortened the processes. Document entry was automated, as the completed paper-based forms no longer had to be manually loaded, rather they are automatically transferred. The digital pen recognises the completed forms thanks to the character recognition. The documents are transmitted and electronically archived. In future, mobile devices could also be used to further automate the processes.
AUTOMATIC MATCHING WITH SUPPLIER PORTALS
HYDAC exchanges various types of containers in cooperation with its customers. Container booking in their portals is a requirement for some of these customers. This was previously a manual effort, which took a great deal of time.
The latest agent technology allowed the supplier portals of a number of major customers to be connected. The obligatory daily booking of the correct number of containers is now possible automatically with the container management system. The account extracts of the two supplier portals are also accessed automatically and compared with the HYDAC data. Differences are displayed directly, which enables a focus on exceptions. The matches between both accounts are automatically identified; complaints only need to be lodged for deviations.
About HYDAC International GmbH
Industry: Fluid technology in connection with hydraulics, electronics and engineering
Specification: Industrial and mobile hydraulics
Representation: Global production and sales sites
Employees: 7,000 worldwide
Internet: www.hydac.com
EURO-LOG Contact for HYDAC
Ursula Anders
Key Account Manager
EURO-LOG AG
Am Söldnermoos 17
85399 Hallbergmoos-Munich
Phone: +49 811 9595-169
Fax: +49 811 9595-199
E-mail: u.anders@eurolog.com
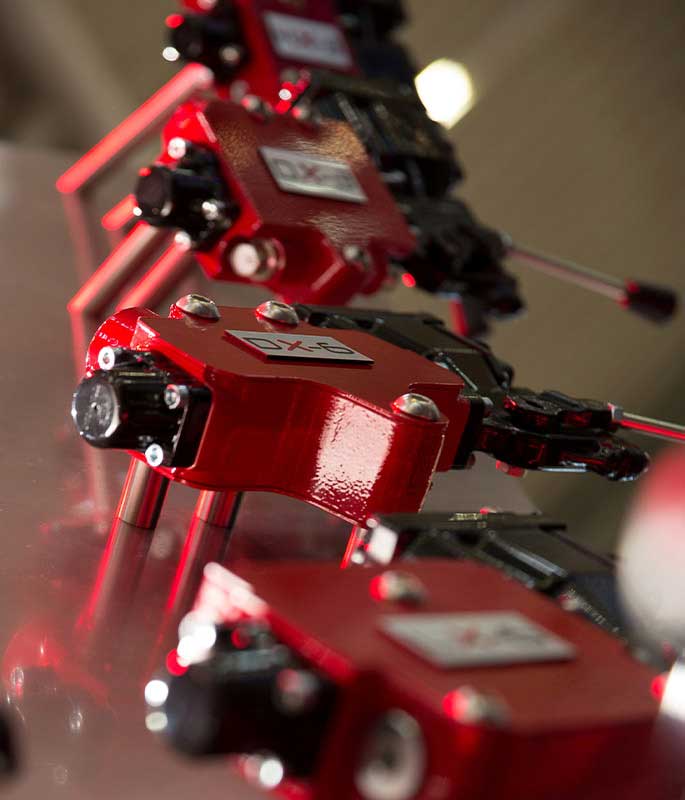
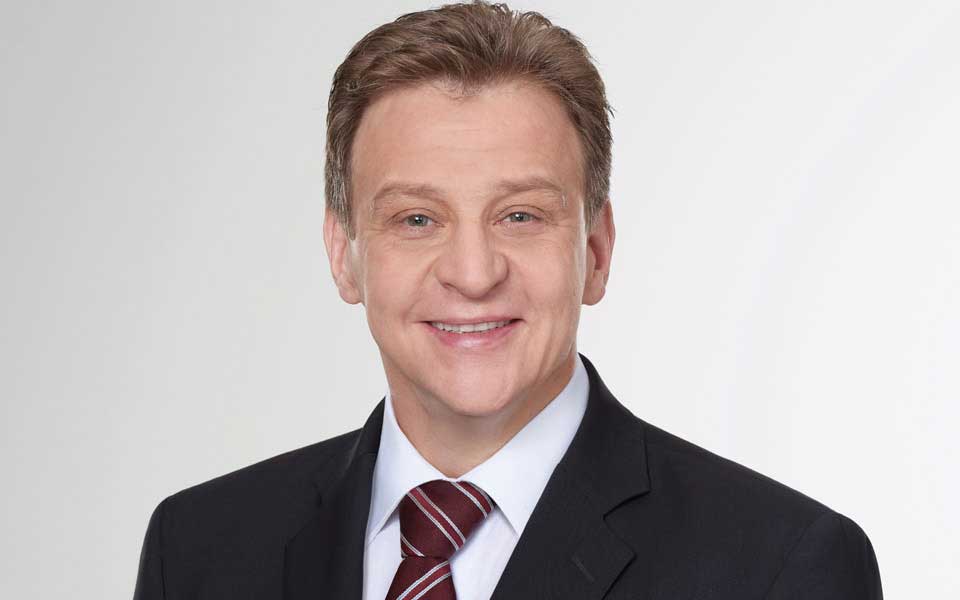
„With the help of EURO-LOG we achieved our goal, transparency over the entire transport network, in a very short time. Within one year a ROI was ensured.“
Armin Bergbauer, CIO Germany & Senior Director Application Development Europe,Ingram Micro Distribution GmbH

„The combination of container management and app helped us to make our container management processes simpler and shorter.“
Thomas Kraft, Managing Director Logistics, HYDAC Verwaltungs GmbH
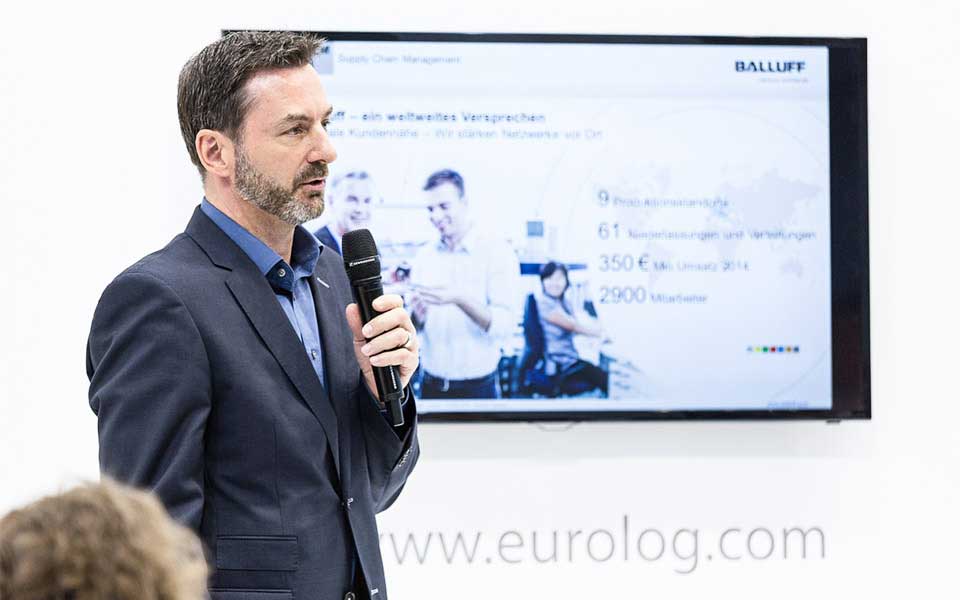
„By integrating ONE TRACK into our website, our customers can be specifically informed about a shipping via e-mail alert.“
Hondo Santos, Director Logistics, Balluff GmbH
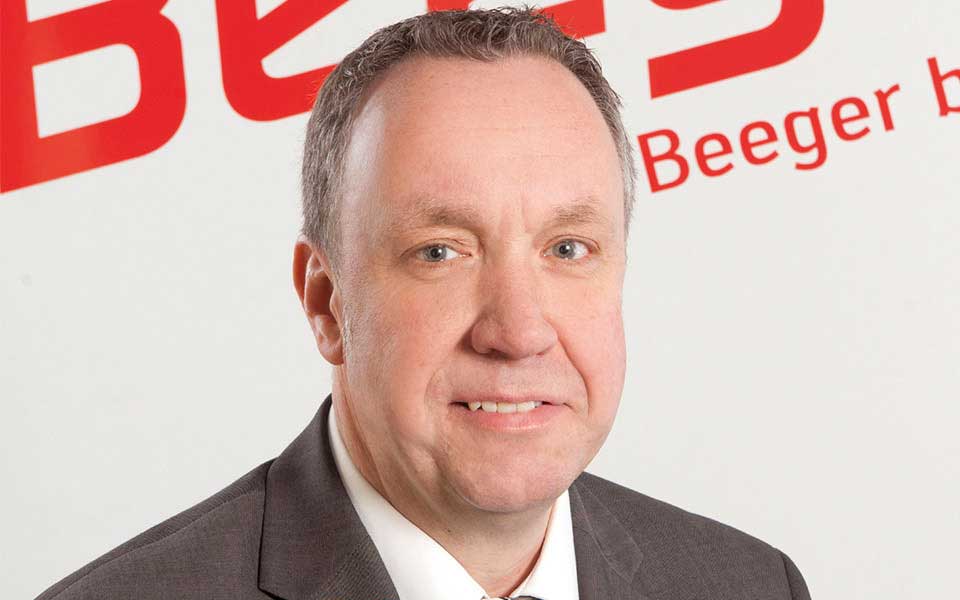
„The smartphones are much more cost-effective than our previous hardware. In addition, the app has been well-received by our drivers since it is very intuitive and easy to use with the clearly understandable icons.“
Frank Reichert, Branch Manager, Beeger Internationale Stückgut Logistik GmbH
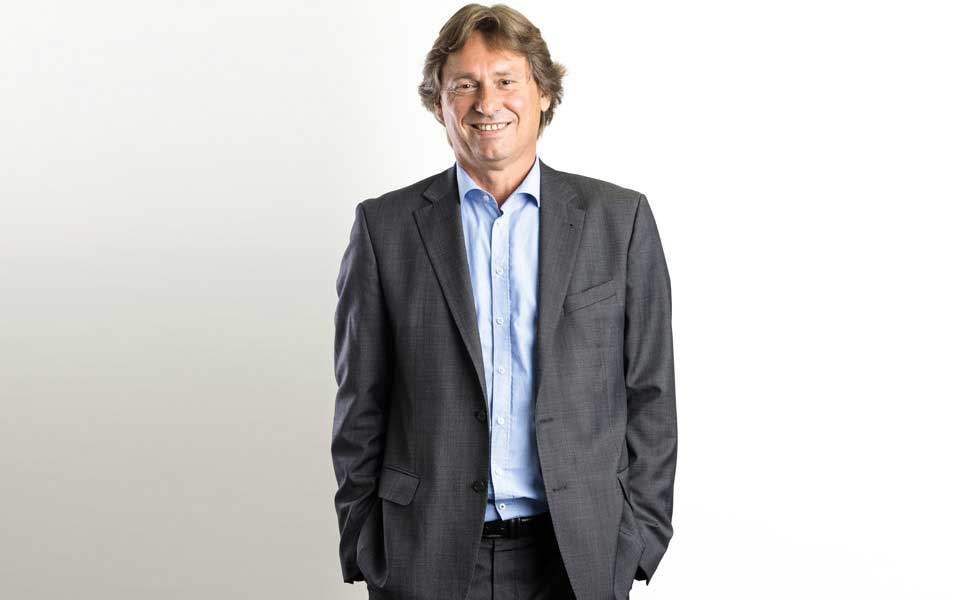
„Mobile Track enabled us to reduce our costs and save on the time and effort of our employees.“
Roland Gigl, former Managing Director, GS Frachtlogistik GmbH
Choose by solutions or industries

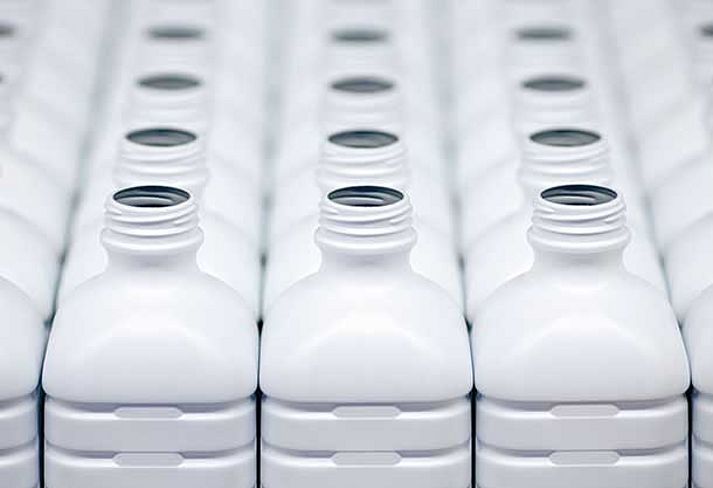
For managing the movements of loading equipment between companies, ALPLA introduces the Container Management system from EURO-LOG.
Cross-company transparency for container movements

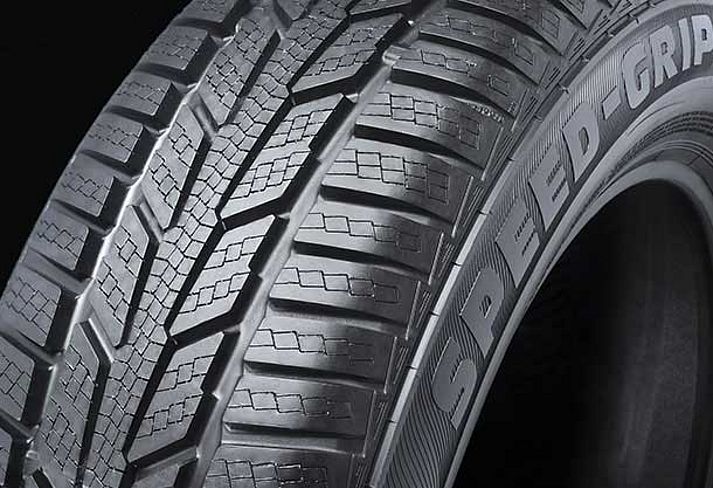
EURO-LOG's container management system enables Continental to control cross-company loading equipment movements right through to the customer.
Continental relies on container management from EURO-LOG


Digitalising the logistics chain creates the transparency needed to elevate cooperation between process partners to the next level.
Connect. Collaborate. Control. EUROLOG SCM Platform














EURO-LOG AG - AM SÖLDNERMOOS 17 - D-85399 HALLBERGMOOS - INFO@EUROLOG.COM - PHONE 0049 811 9595-0