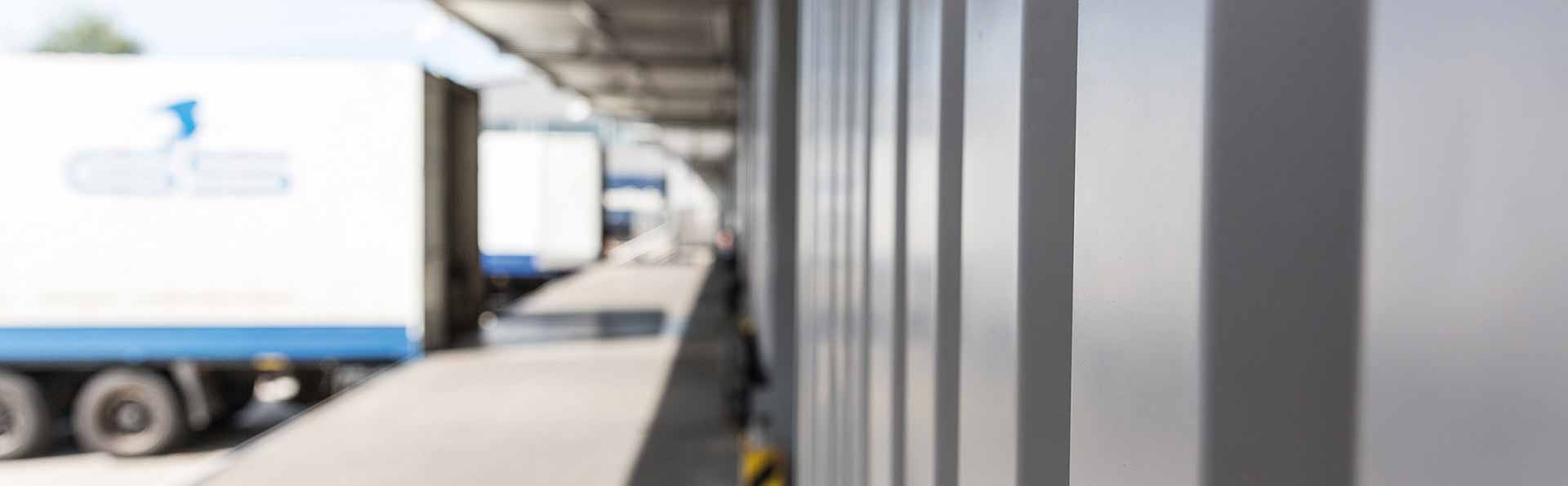
GS Frachtlogistik saves time and money with logistics apps
Drivers can scan package units and the receipt of shipments can be acknowledged by customers via a signature on the smartphone
STARTING SITUATION AT GS FRACHTLOGISTIK
According to GS Frachtlogistik GmbH, one of the greatest challenges for the transport and logistics industry is the digitalisation and simplification of the processes. GS Frachtlogistik has been using scanners for general cargo, partial and full loads as well as for loading and unloading processes in the warehouse since 2000.
In practice, the scanners quickly reached their limits due to their complex architecture and the rigid operating system. GS Frachtlogistik therefore wanted to replace its scanners with a user-friendly solution, which was also mobile. The rapid developments in the area of smartphone technology revealed new potentials in this respect. The scanners were much more vulnerable than the smartphones and app, emphasizes Alexander von Essen, Head of IT at GS Frachtlogistik: “The scanner’s operating system was extremely susceptible to errors. Repairs and software updates were generally complicated, took a long time and were cost-intensive.”
“Mobile Track enabled us to reduce our costs and save on the time and effort of our employees.”
Roland Gigl, Managing Director, GS Frachtlogistik GmbH
THE “MOBILE TRACK” LOGISTICS APP
Since switching to Mobile Track, GS Frachtlogistik has found a cost-effective option for using the latest technologies as well as achieving a high level of acceptance amongst drivers and subcontractors.
- High usability
Thanks to its large and easy-to-understand icons, the app is so easy to use that GS Frachtlogistik saves time (and therefore also money), which the carrier previously had to spend on intensive employee training in the era of the scanners. The easy to understand symbols primarily facilitates the handling of the app for non-native drivers. “The high user-friendliness of Mobile Track allowed us to sharply reduce the training expense for our drivers. For the scanners that were previously in use, we always had to plan several days of induction time”, says von Essen. Tedious installation processes are now also a thing of the past, as the app can easily be downloaded in the Google Play Store and has an “Auto-Deployment” function.
- Durability
The frequency of repair of the hardware was one of the problems with the operating system. Due to their size, the scanners were often put down by employees. This meant, for example, that scanners were placed in the warehouse from time to time, and could quickly be damaged. The workforce is intuitively more careful with smartphones, which can easily be carried in a pocket. This has significantly reduced the costs for repairs and new hardware purchases.
- Transparency and clear map for scheduling
Before implementing Mobile Track, GS Frachtlogistik had no information on the current location of their lorries in use. As Mobile Track regularly sends the geocoordinates of the smartphones to the EURO-LOG data centre, GS Frachtlogistik is informed of the current and previous driver locations. This localisation function is also possible in real-time with the consent of the drivers. The location data is used to clearly indicate where the lorries in use are located in the Mobile Track central system. This enables collection orders required at short notice to be assigned to the closest vehicle. The efficiency of the routes can also subsequently be reviewed. This allows unintentional detours to be identified and avoided, as the carrier sees the routes selected by the drivers or the navigations systems.
- Unburdening of employees, time and cost savings
Before introducing the app, GS employees often had to retrospectively add information, which had been lost by scanner malfunctions. The effort involved was huge, as employees then had to manually enter all missing information based on delivery and cartage notes.
Schedulers are also unburdened during “rush hour”. Previously, they often also had to deal with configuring and replacing several defective scanners in the morning and evening when the drivers arrived on-site for loading and unloading. The carrier’s IT can now also better focus on other topics thanks to Mobile Track, as it no longer has to deal with error analysis and returning defective devices to the manufacturer.
According to GS Frachtlogistik’s estimates, Mobile Track has allowed the logistics service provider to save around one man-hour per day and therefore approximately 7,000 euros per annum compared to the previously used scanners. “Mobile Track enabled us to reduce our costs and save on the time and effort of our employees”, emphasizes Roland Gigl, Managing Director of GS Frachtlogistik.
- Straightforward management of order peaks
GS Frachtlogistik frequently employs external partners to manage order peaks. Before the introduction of the app, there was the following problem:
external service providers that did not own scanners did not want to purchase a device for a period of use of two weeks, for example. By contrast, smartphones are now generally present in every operation. The app can be easily downloaded and the service provider has the necessary tool for their deployment on hand within just a few minutes. Even if the external service provider was prepared to procure a scanner for the short period of time, the induction phase took too long due to the complicated operation of the scanner. This time can now be saved thanks to the ease of use of Mobile Track.
- Electronic data acquisition at a central point
“Another benefit of Mobile Track is that we can record all information electronically at a central point”, says von Essen. For example, the list with shipment information (cartage notes) can be viewed electronically in Mobile Track. Before the introduction of the app, the information was only available on a printed list.
In addition, the app now allows a warning to be displayed to the driver, for example, that they need to confirm the receipt of cash on delivery.
MOBILE TRACK IN PRACTICAL APPLICATION
Upon delivery of the goods, the driver scans the delivered package units and creates a corresponding status (“delivered”). The status contains the date and time of delivery. Moreover, information on the condition of the shipment can also be added. If damage is identified on the shipment, photos for documentation can be taken directly on-site.
The recipient acknowledges the receipt of the goods by providing their signature. This can take place directly on the smartphone, in the app. The recipient’s name and signature as well as the status verify the delivery of the goods and provide “Proof of Delivery” (POD). The delivery documents are automatically transmitted to the in-house system and to the GS Frachtlogistik carrier cooperation, ONLINE Systemlogistik.
However, the use of the signature function is not a mandatory part of the app. If the recipient does not want to provide an electronic signature, the driver has the option of photographing the signature provided on the cartage note.
The scheduling system transmits the delivery orders to the respective driver’s smartphone. The driver then has the option of navigating directly to the relevant delivery or collection address from Mobile Track.
REVOLUTION IN WAREHOUSE SCANNING
Besides Mobile Track, GS Frachtlogistik also uses the EURO-LOG Mobile Scan app for local traffic loading at the warehouse. In future, loading and unloading processes at the warehouse will be recorded in an extended version of Mobile Scan.
Moreover, the app will also run on Android scanners at GS Frachtlogistik, as the volume to be scanned in the warehouse is often not practical for smartphones. In contrast to conventional scanners, the new Android hardware can map the app in exactly the same way as on a smartphone. This means that the clarity and simple operation of a smartphone app is also ensured on a scanner. In addition, the new and improved displays will show the matching processes much better and with improved legibility. In contrast to the mobile phone camera on a smartphone, a scanner’s laser (imager) can manage a larger volume more quickly and easily. This is particularly important in warehouse scanning due to the large number of package units.
In the current development of their hardware, many scanner manufacturers are focussed on making sure that scanners are easier to handle, similar to smartphones. This provides another benefit compared to the old scanners. As part of the further development of its apps, EURO-LOG is therefore aiming to make sure that they work across all hardware. This means that carriers, such as GS Frachtlogistik, are independent of the terminal used and they can choose between smartphones and the new Android scanners.
About GS Frachtlogistik GmbH
Founded in 1991
Part of the Raben Group since July 2016
85 employees, of which 9 are trainees
General cargo, combined transport and logistics
35 vehicles between 3 and 24 tonnes in regional transport
8,000 sqm of storage area at the site in Munich-Garching
7,500 spaces for pallets in the high-bay warehouse
1,000 sqm air freight security area
www.gs-frachtlogistik.de
EURO-LOG Contact for GS Frachtlogistik
Claus Süskind
Head of Sales
EURO-LOG AG
Am Söldnermoos 17
85399 Hallbergmoos-München
Telefon: +49 811 9595-109
Telefax: +49 811 9595-199
E-Mail: c.sueskind@eurolog.com
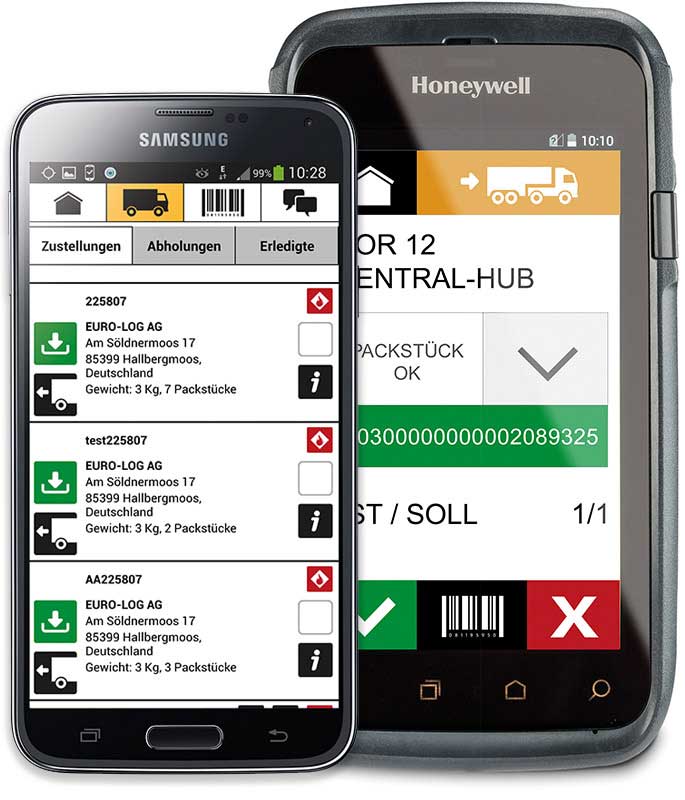
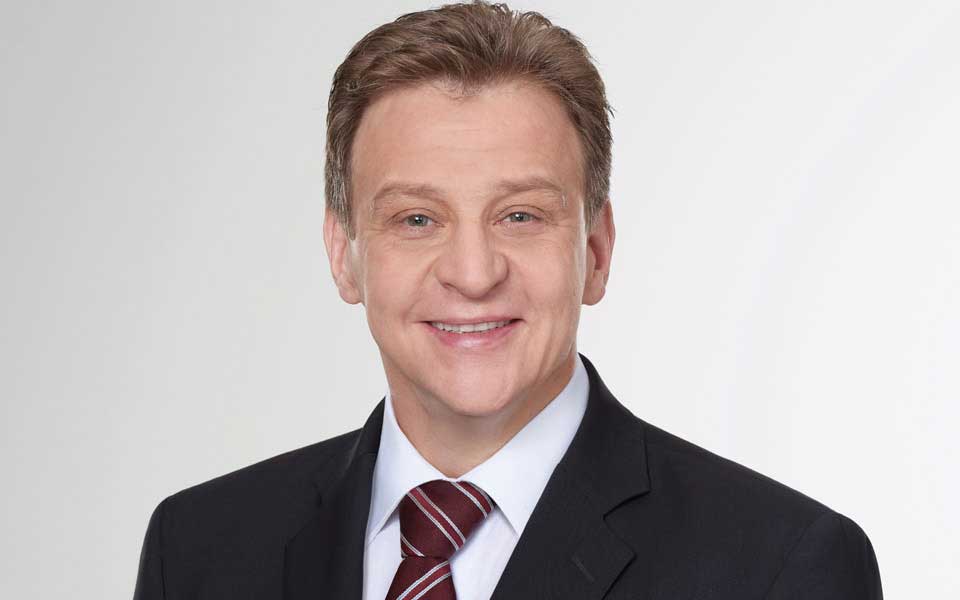
„With the help of EURO-LOG we achieved our goal, transparency over the entire transport network, in a very short time. Within one year a ROI was ensured.“
Armin Bergbauer, CIO Germany & Senior Director Application Development Europe,Ingram Micro Distribution GmbH

„The combination of container management and app helped us to make our container management processes simpler and shorter.“
Thomas Kraft, Managing Director Logistics, HYDAC Verwaltungs GmbH
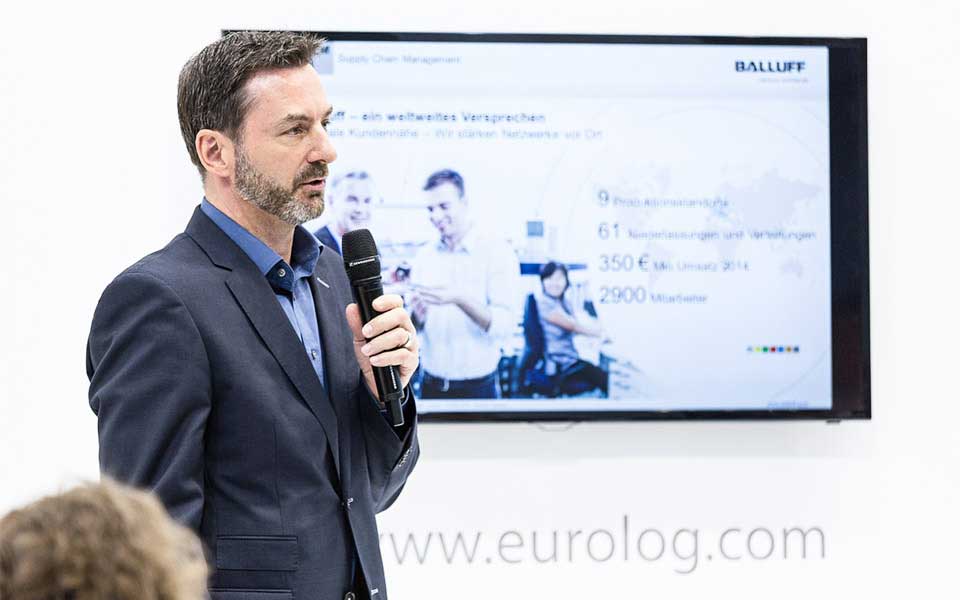
„By integrating ONE TRACK into our website, our customers can be specifically informed about a shipping via e-mail alert.“
Hondo Santos, Director Logistics, Balluff GmbH
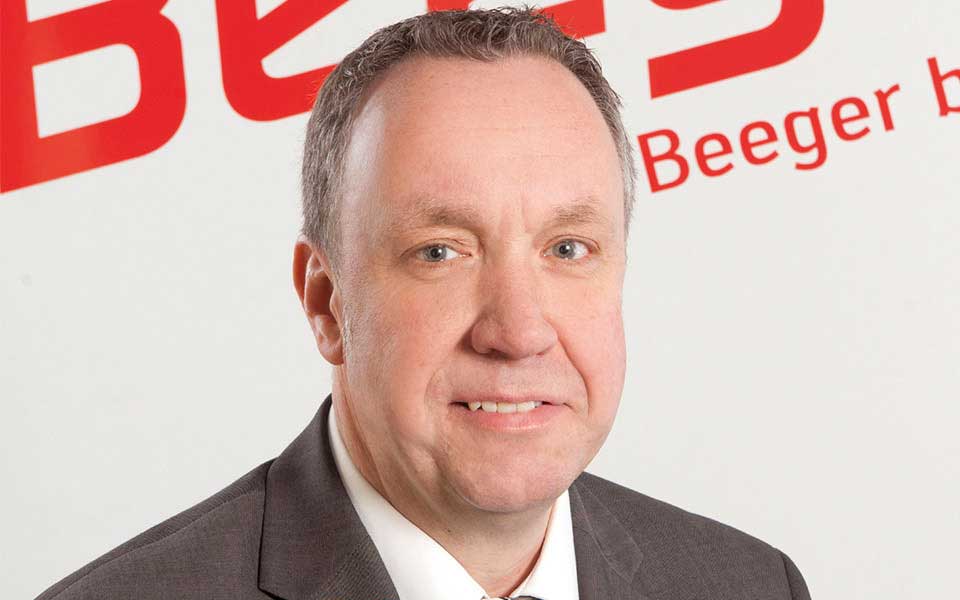
„The smartphones are much more cost-effective than our previous hardware. In addition, the app has been well-received by our drivers since it is very intuitive and easy to use with the clearly understandable icons.“
Frank Reichert, Branch Manager, Beeger Internationale Stückgut Logistik GmbH
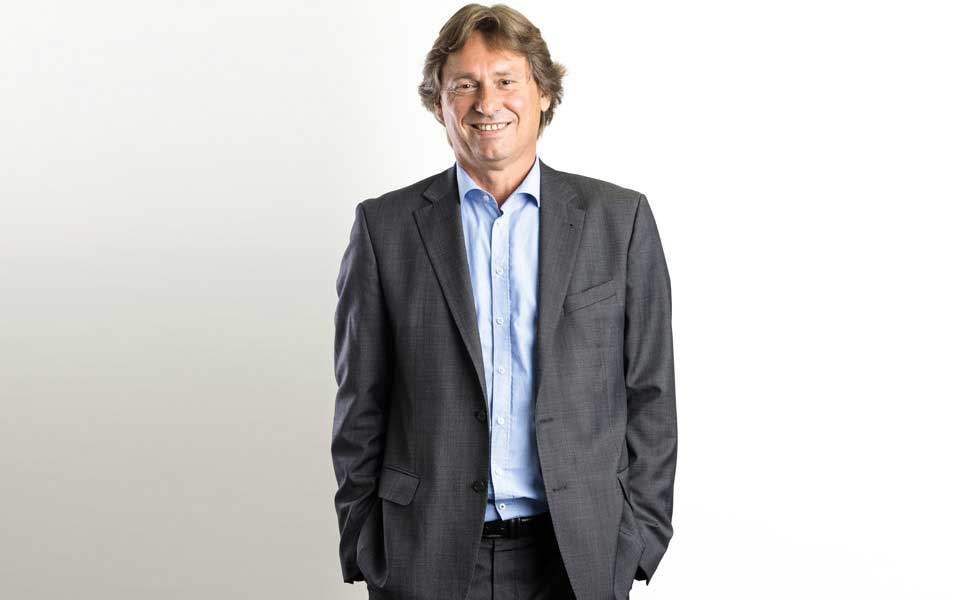
„Mobile Track enabled us to reduce our costs and save on the time and effort of our employees.“
Roland Gigl, former Managing Director, GS Frachtlogistik GmbH
Choose by solutions or industries

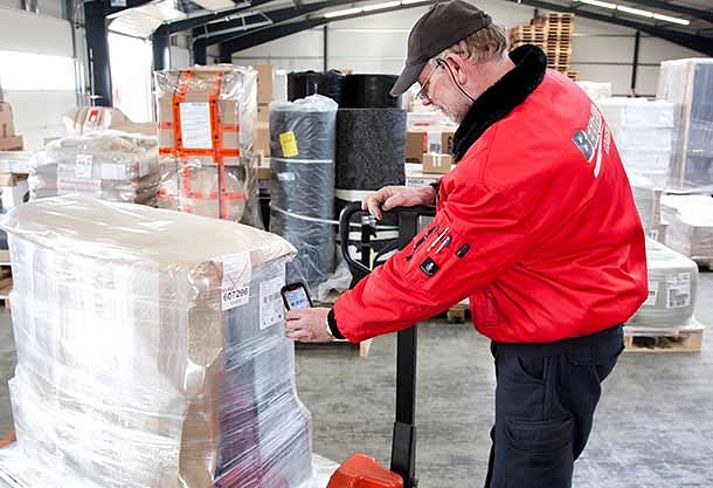
Logistics service provider beeger switches to a cost-effective and straightforward system for collection and delivery scanning.
Cost savings thanks to the mobile track logistics app

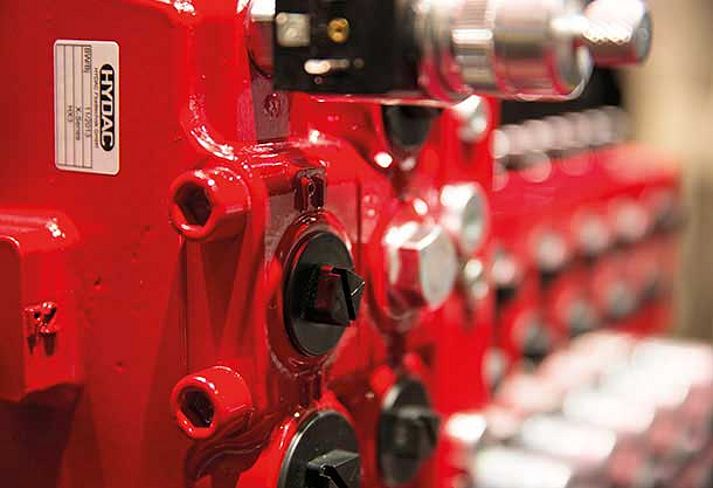
HYDAC achieves a company-wide view of the physical inventories of in-house and customer containers.
Comprehensive container management at HYDAC


Digitalising the logistics chain creates the transparency needed to elevate cooperation between process partners to the next level.
Connect. Collaborate. Control. EUROLOG SCM Platform








EURO-LOG AG - AM SÖLDNERMOOS 17 - D-85399 HALLBERGMOOS - INFO@EUROLOG.COM - PHONE 0049 811 9595-0